2011/7/21 Braskem
Braskem to acquire
naphtha made from post-consumption recycled plastic
Partnership with Novaenergia returns to the production cycle 36 tons of recycled plastic per
day in the form of light oil
As of 2013, Braskem will
have yet another alternative feedstock source. In addition to
sugarcane ethanol, which is used to make green plastic, the
company will begin using naphtha made from post-consumption
recycled plastic. The
product will be supplied by Novaenergia, a
company from the Wastech group located in Bahia state
specializing in waste treatment, which will build its first
advanced recycling plant along Cia Aeroporto Highway in Salvador,
Bahia.
Braskem is expected to acquire initially 1.4 million liters
of naphtha
made from plastic waste per year, which will be processed at its
Basic Petrochemicals Unit in the Camaçari Complex. "Seeking out new
technologies and feedstocks that generate lower environmental
impacts is part of Braskem’s commitment to the sustainability
of the plastics production chain," explained Hardi Schuck,
Braskem’s Supply Chain Officer.
Another advantage
of the project is its contribution to post-consumption recycling
in major cities, which is still a challenge in Brazil.
Novaenergia’s proposal is a sustainable
solution for the destination of waste in Salvador and surrounding
cities, which currently generate around 3,000 tons of waste per
day. The plant will process 450 tons of waste per day and will transform plastic waste
into synthetic oil. Every 36 tons of this waste will yield 30,000
liters of light oil per day, which will be used by Braskem to
make
naphtha, as well as fuel oil and diesel oil with low sulfur
content (S<10ppm). With the reuse of this plastic and
the other recyclable materials extracted in the process, the
amount of waste in landfills will decline by 50%.
The installation of Novaenergia’s recycling unit in Bahia will
require investment of some R$ 25 million, with startup expected
by the end of 2012. "Our agreement with Braskem is very
important for the Novaenergia project, since it lends credibility
to the process we are adopting and to the quality of our final
product," said Luciano Coimbra, president of the
Wastech/Novaenergia group.
ーーー
2008/12/22
Wastech invests in
technology for plastic recycling
In spite of offering
advantages in the substitution of some materials, plastic is seen
in many cases as one of the environmental villains. Such
reputation, however, may have its days counted.
If the new recycling
technologies of the product are successful, plastic shall follow
the same path of the aluminum cans, which practically "do
not touch the ground" when they are thrown away.
One of the most recent
techniques, and that may provide additional value to the
recycling of plastic, is being brought to Brazil by Novaenergia, a
company created by the Wastech group. Specialized in the treatment of
dangerous residues, with more than 20 years in the market, the
group entered into an agreement with the German Clyvia
Technology to transform plastic into diesel
oil.
The basic idea is get the
byproduct of oil and by means of processes of fractioned
depolymerization make the opposite way of the plastic
manufacturer, making the material return to its previous
condition. That because the heating of pricked plastic, when
under pressure, leads to a chemical process inside the carbon
chain that allows obtaining, inside a vacuum reactor,
hydrocarbons with low sulfur content, informed, Luciano Costa
Coimbra, a Wastech partner.
Each ton of plastic is
enough to produce ten thousand liters of diesel. "And it is
not biodiesel, we call it ‘liesel', because it is diesel from
mineral raw material, but which will help ‘clean' (limpar, in Portuguese) the
environment", added Coimbra. According to him, diesel made
from plastic can be used in any normal diesel-driven vehicle,
without any adaptation. The agreement foresees the exclusiveness
of the Brazilian company for the use of the technology for five
years and the project includes the implementation of up to 50
recycling units all over Brazil, at an estimate cost of R$ 16
million (US$ 7 million) each. The investments will be made with
its own funds or, in some cases, in partnership with some
national investors interested in the sectors of plastics,
collection and burying of urban garbage and treatment of
industrial residues. The return of the investment is expected to
occur within 30 months. There are negotiations for the sale of
stocks of Novaenergia to some international financial funds
specialized in environmental investments and in the generation of
energy or fuels made from alternative sources, according to
Coimbra. The first four units should be installed in São Paulo, Rio de Janeiro, Minas
Gerais and Bahia. "If everything goes right, garbage will
become a commodity, mainly if we take into consideration that
plastic represents nearly 15% of everything that is thrown
away", added the Wastech partner, company that has contracts
of specialized transport and final disposal of residues of nearly
R$ 25 million (US$ 10,9 million).
ーーー
2006/8/8
Successful Trial of
Clyvia Depolymerization Plant to Convert Waste Oil to Diesel
Clyvia Technology GmbH
has successfully converted 3 tonnes (approximately 3.3 US tons)
of waste oil into 2,000 liters (1.7 tonnes or approximately 528
US gal.) of diesel-like light oil in a large scale trial run of
its pilot fractional deploymerization plant.
In the process, waste oil
is pre-heated to 170° C prior to being fed into the
plant reactor containing a catalyst compound. In the reactor, the
waste oil is brought to a temperature of 400°
C. The light oil
then produced by the reactor process is extracted into a
distillation tower.
The catalytic
depolymerization process used in Clyvia Technology’s pilot plant is similar to the
cracking of crude oil. The thermal treatment process shortens the
long hydrocarbons in the waste to the length of diesel or heating
oil.
The Clyvia process splits
the longer molecules without forming methane, meaning that the
Clyvia system does not produce major quantities of coke. The
system is different from pyrolytic processes used to split
hydrocarbon molecules, which require extremely high reactive
temperatures, significantly increasing the cost of the process,
and producing high amounts of waste carbon byproduct.
Initial
gas-chromatographic tests conducted by Clyvia Technology have
shown that the oil produced by the trial contain the expected
distribution of diesel hydrocarbon chains. Density measurements
conducted by Clyvia Technology have also been positive, according
to the company.
Clyvia Technology has
submitted the diesel output produced during the trial run to an
external independent laboratory where it will be tested to check
if it complies with diesel norm DIN EN 590 (the European standard
for diesel fuel).
Tests of earlier output
did not produce diesel fuel meeting low-sulfur requirements,
although it did meet “most” of the fuel parameters required
under international fuel standard DIN 51603-1, according to
Clyvia’s most recent annual report. (Earlier post.)
The current round of
development and testing in the new pilot plant are focused on
producing diesel fuels that meet necessary sulfur content
requirements.
2012/8/31 European Plastics News
Braskem inaugurates PVC plant
Braskem SA has inaugurated a PVC resin plant
in Brazil that the group says is the largest in Latin
America.
The plant in Marechal
Deodoro, Alagoas state, has annual production capacity of
200,000 metric tons.
The Aug. 17 inauguration ceremony was
attended by Dilma Rousseff, Brazil’s president, and Teotonio Vilela Filho, the
governor of Alagoas.
“The inauguration of this unit is fundamental
for meeting demand from our Clients throughout Brazil operating in strategic
sectors of the economy, such home building, sanitation and infrastructure. With
this new plant, we reaffirm our commitment to the development of both the state
of Alagoas and Brazil,” said Carlos Fadigas, Braskem’s CEO.
The plant, which took two years to build,
will create 10,000 direct and indirect jobs.
The investment of 1 billion real ($488
million) in the plant is the largest ever made for a single project since
Braskem was founded 10 years ago.
2013/12/11 Braskem
Braskem and
Genomatica sign an agreement for the development of green butadiene
Braskem, the world's largest biopolymers
producer, strengthens its commitment to the research of renewable
feedstock-based chemicals
Braskem, the
largest petrochemical producer in the Americas and the world's leading
biopolymer producer, and Genomatica, a U.S.
biotechnology company, have signed an agreement for the joint development of
a new technology for the production of butadiene from
renewable feedstocks. Through this partnership, Braskem reaffirms its
commitment to invest in the research of producing chemicals from renewable
feedstocks, effectively strengthening its leadership role in this segment.
Braskem's
objective with green butadiene is to primarily serve the synthetic rubber
market, whose demand is currently met by naphtha-based butadiene, of which
the company is already the world's third-largest producer. With the
expectation of a recovery in global economic growth over the coming years,
our forecast calls for growing demand for butadiene based elastomers by tire
manufacturers, who are the largest consumers of butadiene.
The research
program conducted jointly by Braskem and Genomatica will seek not only to
find alternatives that are based on renewable feedstocks, but on developing
routes that are also competitive in terms of production cost. Braskem,
together with Genomatica, will dedicate a team of researchers to the
development of this technology. Under the agreement, provided the results
are successful, Braskem and Genomatica will build pilot and demonstration
plants. The agreement gives Braskem certain exclusivity rights to the
technology's use in the Americas.
"Braskem has
a clear strategy for investing in the research and development of renewable
based chemical technologies as alternatives to complement our current
product portfolio based on petrochemicals. In 2010, we became the world
leader in Biopolymers when we announced the production of plastic made from
sugarcane, and we are now further reinforcing this vision," said Alexandre
Elias, director of Renewable Chemicals at Braskem.
According to
Christophe Schilling, CEO of Genomatica, the agreement will help strengthen
their position as a developer and licensor of bio-based process technologies
to chemical manufacturers. "Our partnership brings the industry closer to
commercializing a more sustainable and cost-predictable butadiene", said
Schilling. Genomatica, which was founded in 1998 by
researchers from the University of California, San Diego (UCSD),
holds 71 issued patents and 450 additional patent applications and has been
applying its intellectual property and technology platform to develop
multiple approaches for the commercial production of bio-based butadiene,
using multiple renewable feedstocks.
In addition
to serving as a raw material for the tire industry, butadiene based
materials are also used in home appliances, footwear, plastics, asphalt
modifiers, oil lubricant additives, tubing, construction components and
latex. Butadiene produced by traditional technological routes has suffered a
structural shortage in the Americas due to the growth of shale gas, which,
unlike naphtha, generates almost no co-products.
Green
Plastic
Since
September 2010, Braskem has produced polyethylene resin made from sugarcane
ethanol on an industrial scale, which is a 100% renewable material. It
invested R$500 million in the construction of a plant located in the Triunfo
Petrochemical Complex in the South of Brazil with a capacity to produce 200
kton of green plastic annually. Braskem's green plastic is a milestone in
global innovation, making Brazil the leading producer of biopolymers in the
world. Identified by the "I'm greenTM" seal, the green polyethylene
developed in Brazil is used to make a wide range of food packaging and
consumer goods.
Genomatica
Our GENO BDO™ process is for the
production of BDO, an intermediate chemical used in everyday products
including athletic apparel, running shoes, electronics and automotive
applications.
Our GENO BDO process is now commercial. Our process was used to produce
5 million pounds of BDO in late 2012, all sold and shipped; and has been
licensed by BASF, the world’s #1 chemical producer and #1 BDO producer,
as well as by Novamont in Italy.
三菱化学は米国のGenomatica社と戦略的提携で合意した。
Genomaticaが開発した植物を原料に1,4-ブタンジオールを製造する技術に、三菱化学の技術を組み合わせ改良した技術を用いて、中東、インドを含むアジアでの1,4-ブタンジオール事業化を検討する。
----------
In August 2011, we announced
that we had successfully produced butadiene from renewable feedstocks in
pound quantities.
In April 2013, Versalis and Genomatica announced an agreement to create
a joint venture for butadiene. The two companies will work together to
develop a complete ‘end-to-end’ process for the on-purpose production of
butadiene from non-food biomass.
Versalis, formerly known as Polimeri Europa, is the largest Italian
chemical company and a subsidiary of ENI.
Versalis, formerly known as Polimeri Europa, is the largest Italian
chemical company and a subsidiary of ENI. - See more at: http://www.genomatica.com/partners/versalis/#sthash.WuzV10o7.dpuf
In December 2013, Braskem and
Genomatica announced a joint development agreement for butadiene.
Braskem anticipates funding Genomatica’s development work; will allocate
Braskem R&D resources; and fund the construction of pilot and
demonstration-scale plants.
September 9, 2014
Braskem Joins Amyris and Michelin to
Accelerate the Industrialization and Commercialization of Renewable
Isoprene
Partnership Aims to Develop and Produce Renewable Isoprene
for Production of Tire and Other Rubber Applications
Amyris, Braskem and Michelin announced today that Braskem is joining
the ongoing collaboration between
Michelin and Amyris. This collaboration was initiated to develop and
commercialize renewable isoprene, sourced from various biomass as an
additional sustainable pathway to produce isoprene.
Under the terms of the agreement, Braskem, Michelin and Amyris will work
together to develop a technology to utilize plant sugars, such as those
found in Brazilian sugarcane or cellulosic feedstocks, to produce
renewable isoprene. Adding the expertise of Braskem, the largest
petrochemical company in the Americas and global leader in the
production of biopolymers, Amyris and Michelin will accelerate the
industrialization of renewable isoprene.
Amyris will share its
rights to commercialize the renewable isoprene technology developed
under this collaboration with Braskem.
Michelin will maintain certain preferential, but not exclusive, access
to the renewable isoprene to be produced by this technology.
The companies will not disclose details of the agreement, including the
financial contributions of each party.
This joint project, with Amyris and Braskem, will give Michelin an
additional sustainable sourcing channel for poly-isoprene for the
production of quality tires, providing a high-performance,
environmentally responsible material.
"With this new partnership, we join forces with Amyris and Michelin in
the development of an innovative technology that strengthens our
commitment to improve people's lives, creating solutions through
sustainable chemistry," said Luciano Guidolin, Vice President for
Polyolefins and Renewables of Braskem. With a proven track record in
leading research in sustainable chemistry, Braskem has already an
experience in the development of 100% renewable polyethylene.
"Braskem is an ideal partner to join our isoprene project with Michelin.
They bring the right expertise and share in our commitment to transform
the chemical industry through sustainable product innovation and
superior performance," said John Melo, President & CEO of Amyris. "Amyris
has led the way in producing long-chain hydrocarbon molecules via
fermentation, from anti-malarial drug precursors to long-chain
hydrocarbon molecules used in cosmetic emollients and even
fuels.Building on the success of this proven technology to produce
tailored hydrocarbons, we are revolutionizing the way products are made,
one molecule at a time," concluded Melo.
"We are pleased to have a strong industrial partner join our ongoing
collaboration with Amyris. Braskem's chemical industry experience,
coupled with Amyris's biotechnology expertise, will support Michelin's
goal of addressing the long-term needs of the tire industry for
sustainable sourcing with renewable chemicals," said Jean-Christophe
Guerin, Head of the Materials Division of Michelin.
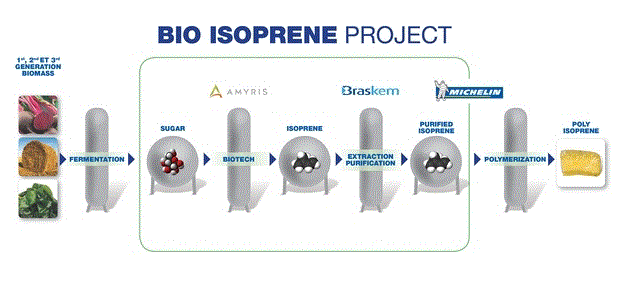
ーーー
Amyris, Inc., a leading renewable
chemicals and fuels company, and Michelin, a leading innovator in the
tire industry, announced that the two companies have signed a definitive
agreement to collaborate in the development and commercialization of
Amyris No Compromise®
renewable isoprene, the chemical building block in rubber tires and
other products that use synthetic and natural rubbers.
Under the agreement, Amyris and
Michelin will partner to contribute funding and technical resources to
develop Amyris’s technology to produce isoprene from renewable
feedstocks. Amyris expects to begin commercializing this isoprene in
2015 for use in tire and other specialty chemical applications such as
adhesives, coatings and sealants. Michelin is committed to off-take
volumes on a ten-year basis. In addition, Amyris retains the right to
market its renewable isoprene to other customers.
“This partnership will allow both
companies to continue Michelin’s tradition of innovation in the tire
industry and expand Amyris’s industrial biotechnology platform for new
products,” said John Melo, CEO of Amyris. “Growing demand for isoprene
and a desire to increase the sourcing of sustainable raw materials
create a great opportunity for Amyris to bring to market renewable
solutions with No Compromise® performance that also
reduce price volatility.”
Amyris’s technology, currently used
to produce at commercial scale a 15-carbon molecule called farnesene,
can also convert plant-based sugars into isoprene, a 5-carbon molecule
and main ingredient in the production of synthetic rubber. Isoprene has
traditionally been produced as a by-product of the thermal cracking of
naphtha to produce ethylene or via C4 refinery stream synthesis. As the
petrochemical industry adjusts to lighter cracking slates with the
advent of shale gas, new sources of isoprene have become necessary.
Amyris is an integrated renewable
products company focused on providing sustainable alternatives to a
broad range of petroleum-sourced products.
Amyris uses its industrial bioscience technology platform to
convert plant sugars into a variety of hydrocarbon
molecules -- flexible building blocks that can be used in a wide
range of products. Amyris is commercializing these products both as
No Compromise® renewable ingredients in
cosmetics, flavors and fragrances, polymers, lubricants and consumer
products, and also as No Compromise renewable diesel and jet fuel.
Amyris Brasil Ltda., a subsidiary of Amyris, oversees the establishment
and expansion of Amyris's production in Brazil.
Amyris は2003
年に設立され、サンフランシスコ郊外に拠点を置くバイオ分野の先端技術開発企業で
、同社のバイオ製品は、香料、化粧品やパーソナルケア、さらにはプラスチック添加剤やディーゼル燃料やジェット燃料など、幅広い用途に展開されている。
Amyrisはバイオ由来の新規ジエンモノマー Farnesene (商品名
Biofene) を開発した。
Amyris の
trans-β-Farnesene
は糖類をイーストで発酵させてつくる。
イーストのメタボリズムを変え、エタノールをつくるものをハイドロカーボンをつくるものに変換した。

Amyris’s initial portfolio of
commercial products is based on Biofene, Amyris’s brand of farnesene, a
long-chain branched hydrocarbon, manufactured using our engineered
microbes in fermentation.
Our product portfolio is divided in these market segments:
・Cosmetics
・Flavors & Fragrances
・Polymers & Plastic Additives
・Home & Personal Care
・Lubricants
・Fuels
製造工場はブラジル(town of Brotas in
southeastern Brazil) 200,000L x 6
のFermentation
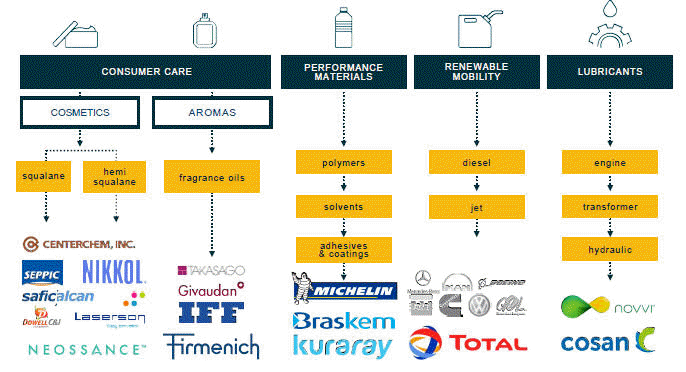
2014/5/1
クラレ、バイオ系液状ゴムの開発に向け、米国のAmyris
Inc.との提携強化
2014/7/14 高砂香料、フレグランス新素材開発でアミリス社と提携
高砂香料工業は米国のAmyris
Inc.と共同開発中のファルネセンを出発原料とした新規フレグランス原料について、将来の商業化への第一歩として、スケールアップ試作のためアミリスからファルネセンを購入する運びとなりました。高砂香料工業はアミリスが有する糖類から種々の化合物へと変換可能な工業的合成生物学技術を活用し、イノベイティブで競争力があるサステナブル香料原料のサプライヤーとなるべく、2012年末からアミリスとの提携を開始しました。
米Amyris社は2014年6月8日、ファルネセン(farnesene)由来の芳香性分子を商業化するため、高砂香料との関係が次の段階に進展したと発表した。
July 31, 2014 First International
Commercial Flight Completed With Newly Approved Amyris-Total
Aviation Biofuel
Yesterday, Amyris, an
industrial bioscience company, partnered with Brazilian airline,
GOL, to fly the industry's first
commercial flight with farnesane, the recently approved
renewable jet fuel. The first flight, GOL flight 7725, departed
from Orlando, Florida on July 30, 2014 at 5:15 PM ET and
traveled to Sao Paulo, Brazil.
Earlier this month, GOL
committed to fly its Boeing 737 fleet with up to a 10 percent
blend of the renewable farnesane fuel starting with this initial
flight on July 30, 2014. Farnesane can reduce greenhouse gas (GHG)
emissions by up to 80 percent compared to petroleum fuels. When
blended with Jet A/A1 fuel at 10 percent, farnesane can also
reduce particulate matter emissions, decreasing pollution near
airports and major metropolitan areas.
2014/6/16
With the newly revised ASTM
standard for jet fuel, Amyris and Total today begin to prepare
to market a drop-in jet fuel that contains up to 10% blends of
renewable farnesane.
Developed by Total and Amyris,
this new jet fuel blend meets the rigorous performance
requirements set for Jet A/A-1 fuel used by the global
commercial aviation industry.
Founded in 2003 in the San Francisco Bay Area by a group of
scientists at the University of California, Berkeley, Amyris
uses breakthrough science and an innovative business model
to address some of our planet’s most daunting problems.
Amyris’s first major milestone came in 2005 when, through a
grant from the Bill & Melinda Gates Foundation, our
scientists developed technology capable of creating
microbial strains to produce artemisinic acid
アルテミシン酸—
a precursor of artemisinin, an effective
anti-malarial drug. Malaria is
a preventable, curable disease that claims the lives of more
than half a million people a year.
In 2008, we entered into an agreement with Sanofi-Aventis to
license Amyris technology a royalty free basis for the
purpose of manufacturing and commercializing artemisinin-based
drugs for the treatment of malaria. In 2013, Sanofi began
large-scale industrial production of Artemisinin utilizing
Amyris designed strains. Amyris remains committed to
expanding the reach of anti-malarial treatments, and its
founders have helped establish a non-profit called Zagaya.
Building on this success, Amyris has been applying its
industrial synthetic biology platform to provide
alternatives to a broad range of petroleum-sourced products.
Amyris has focused its development efforts on the production
of Biofene, Amyris's brand of
renewable farnesene, and on delivering a renewable
alternative to petroleum-sourced fuels and chemicals.
After a series of successful rounds of venture capital
funding supported the development of early stages of our
proprietary industrial synthetic biology platform, Amyris
undertook an initial public offering in September 2010.
Amyris shares are traded in the NASDAQ exchange under the
symbol AMRS.
To support our initial commercial production, Amyris
leveraged contract-manufacturing capabilities to begin
producing Biofene at various sites around the world.
Amyris’s first purpose-designed, industrial-scale Biofene
plant located Brotas, São Paulo,
in the southeastern Brazil, began commercial production in
early 2013.
Amyris remains focused on developing its core technology to
produce renewable products to the world, starting with
products derived from Biofene. With about 400 employees
today and millions of dollars invested, Amyris remains a
breakthrough renewable products company built on a
foundation of disruptive innovation for the greater good. |
Dec 25, 2016
Brazilian companies to pay combined $3.5B in bribery case
Brazilian construction conglomerate Odebrecht
and major petrochemical company Braskem have
agreed to pay a combined penalty of at least $3.5
billion to settle allegations that they bribed
government officials in a dozen countries around the world, U.S.
authorities said Wednesday.
The Brazilian corporations admitted to paying hundreds of millions of
dollars in bribes, money that law enforcement officials say was authorized
at the highest corporate levels and was concealed through shell companies
and offshore entities. Both companies have pleaded guilty to bribery-related
charges in federal court in New York and have resolved
charges from the authorities in Brazil, Switzerland and the U.S.
The Justice Department called it the largest resolution ever under the
Foreign Corrupt Practices Act, a 1977 law that
makes it illegal to bribe foreign government officials for business.
U.S. law enforcement officials say bribes totaling about $788 million were
paid since 2001 in connection with approximately 100 projects around the
world, including to secure public works contracts in Panama, Peru, Angola
and several other countries. Some of the offshore entities that were used to
hold and disburse the funds were owned or operated by people in the U.S.,
and some meetings where the scheming occurred took place in Miami, federal
prosecutors said.
Court documents allege that Odebrecht created a stand-alone unit, called the
Division of Special Operations, that “effectively functioned as a bribe
department” within the company and that relied on an off-the-books
communication system of secure emails, code names and passwords.
“Odebrecht had a division in its company dedicated solely to bribery, a full
team of people dedicated to criminal conduct,” FBI assistant director
Stephen Richardson told reporters in a conference call.
The companies have both agreed to cooperate with law enforcement, including
in investigations into individual company officials. They’ve also agreed to
be under the watch of independent compliance monitors for the next three
years.
In a statement Wednesday, William Burck, a lawyer for Odebrecht, said the
company was “glad to be turning the page and focusing on its future.”
Earlier this month, the company apologized for its involvement in corruption
scandals that led to the arrest of its former chief executives and several
of its officials. It acknowledged having made serious mistakes and promised
not to rely on extortion or bribes to get contracts from public officials.
Odebrecht signed another agreement with Brazilian authorities to return
almost $2 billion to public coffers.
The company is at the center of the mushrooming probe at state-run oil giant
Petrobras, which has ensnared Brazilian politicians and business people
across the board.
Some of the corrupt payments alleged Wednesday went to Petrobas employees
and executives, and to political parties and government officials in Brazil,
the Justice Department said. Prosecutors also accused Odebrecht of
conspiring with other Brazilian construction companies to rig bids for
Petrobas contracts.
Dozens of Odebrecht executives signed plea bargains with Brazilian
prosecutors and as many as 200 politicians might be implicated in the
corruption scandal. The company has fired 51 people who participated in the
misconduct and disciplined an additional 26, according to the Justice
Department’s plea agreement.
Plea bargain testimony obtained by The Associated Press cites Brazilian
President Michel Temer 44 times, with accusations of illegal campaign
financing that put his embattled administration at an even bigger risk of
ending within months.
The 82 pages of testimony by former Odebrecht director Claudio Melo Filho
include allegations that Temer illegally financed his campaign in 2014. If
the accusations are confirmed by Brazil’s top electoral court next year, the
president will be removed and Congress will pick a successor. In May,
President Dilma Rousseff was impeached for breaking fiscal rules.
It is not clear whether U.S. prosecutors will be able to bring criminal
charges against individual executives or employees implicated in the
corruption, though they will likely face pressure to do so. A memo last year
from Deputy Attorney General Sally Yates reminded Justice Department
prosecutors that they should strive when possible to hold individuals
accountable for corporate misconduct.
June 22, 2017
Braskem Approves Construction of Delta, the Largest Polypropylene Production
Line in the Americas in La Porte, Texas
Braskem, the leading thermoplastics resins producer in the Americas, today
announces that the Company's Board of Directors has formally approved the final
investment decision to proceed with the largest polypropylene (PP) production
line in the Americas. Braskem will commit up to $675
million in investment capital towards the design and construction of the
new facility which will be named Delta and will be located next to Braskem's
existing production facilities in La Porte, Texas, U.S.
Fernando Musa, Braskem Chief Executive Officer, stated, "Our approval to proceed
with the capital investment in Delta is the latest major milestone in Braskem's
global growth strategy. This new world-class petrochemical facility will bring
important new North American production capacity to help us meet the growing
demand from our clients, reaffirming our position as the leading producer of
polypropylene in the Americas and the third largest in the world."
"Leveraging the success of shale gas energy production, North America has among
the most attractive feedstock profiles worldwide in terms of access to low cost
sources of feedstock and the depth of suppliers. With no new polypropylene
plants added since 2005, North America also transitioned to being a net importer
of polypropylene in 2016. As such, our additional investment in the United
States is a logical extension of our global growth strategy. By increasing our
production capacity in close proximity to customer demand, attractive feedstock
as well as established export channels, we believe Delta will serve our clients
well and offer an attractive return on our investment for our shareholders. This
investment is a true vote of confidence in the future of Braskem and a testament
to our commitment to meeting our clients' needs," concluded Mr. Musa.
With the engineering design phase well underway, the new production line will
have a manufacturing capacity of 450 kilotons (kt),
or the equivalent of approximately 1 billion pounds, per year. Construction will
take place on part of the approximate 200 acres of land at Braskem's current La
Porte facility footprint which is located 26 miles from Houston. The new line
will represent additional production capacity of homopolymers, random
copolymers, impact copolymers, and reactor TPOs, building upon
Braskem's current polypropylene production plant in La
Porte which has a production capacity of 354 kt annually and will
continue operations. Today's announcement also builds upon the momentum of
Braskem's recent launch of its new UTEC Ultra High Molecular Weight Polyethylene
(UHMWPE) production plant located at the same La Porte site.
Delta will benefit from significant existing support infrastructure already in
place to accommodate the new line including feedstock and utilities
connectivity, rail infrastructure, central control room and testing facilities,
emergency response equipment, waste treatment facilities and more.
The construction of Braskem's new Delta PP production line is expected to
positively impact economic activity in the region, employing approximately 1,000
development and construction workers to fully construct the facility. Upon final
completion, the company expects the new line to bring an additional 50 Braskem
permanent full-time jobs to the La Porte community.
Construction is expected to begin mid-summer, with the final phase of main
construction targeted for the first quarter of 2020. The facility design is
being developed directly in-line with Braskem's commitment to sustainability and
attention to eco-indicators such as emissions, water and energy efficiency, as
well as recycling and waste reduction.
Braskemの米国のPP能力 (千トン)
|
既存 |
新設 |
Marcus Hook,
Pennsylvania |
350 |
|
Kenova - Neal, West
Virginia |
240 |
|
La Porte, Texas |
354 |
450 |
Freeport - Oyster
Creek, Texas |
320 |
|
Seadrift,
Texas |
225 |
|
合計 |
1,489 |
450 |
July 25, 2019
Braskem Said to be Withdrawing from
West Virginia Cracker Project
Plans for a multi-billion dollar
ethane cracker in West Virginia are once again uncertain, as Braskem
SA confirmed late Wednesday that it has hired a financial adviser to
evaluate strategic alternatives for a nearly 400 acre site it owns
in the state.
ブラジルのBraskemの親会社のOdebrecht は2013年末に、SABIC Innovative
PlasticsからWest Virginia州 WashingtonにあるSABIC Innovative
Plasticsの工場用地を11百万ドルで購入し、最近登記された。
工場はOhio州との州境のオハイオ川沿いに立地し、Marcellus
Shaleエリア内にある。
SABIC Innovative Plastics は2013年11月にこの工場を2015年に閉鎖すると発表している。
同社では熱可塑性樹脂の米国での生産統合を図っており、この工場での生産は2015年にイリノイ州Ottawaとミシシッピー州Bay
St. Louisに移す。
Odebrecht
は2013年11月に同州知事と共同で、同地にエタンクラッカーと3つのPEプラント及び水処理、コジェネレーションなどの付帯設備を建設する計画を発表した。この計画はAppalachian
Shale Cracker Enterprise(略称 Ascent)と呼ばれる。
この計画は最終決定されていないが、土地の買収が明らかになったことで、今後計画が進行すると期待されている。
Odebrechtが全体の計画と資金及び水処理、コジェネレーションを担当し、Braskemが石油化学関連を担当する。
INEOSは2014年10月1日、Ascent
Project にInnovene S PEと Innovene G PE 技術を供与する契約を締結したと発表した。
2014/1/22
Braskemの米国エチレン計画、エタン原料とメタン原料
Braskem America spokesperson
Stacy Torpey said the company is exploring its options for the
property along the Ohio River where plans for a large cracker were
announced in 2013. She said the company has received a “number of
recent inquiries” about the site, prompting the company to consider
a possible sale.
The project, announced by former
Gov. Earl Ray Tomblin’s administration, was to include three
polyethylene plants, water treatment infrastructure and a power
plant. But it has faced persistent delays since it was announced. In
2015, Braskem said it was putting plans for the facility on hold
pending further project analysis amid a severe commodities downturn
that roiled the oil and gas industry.
Rumors of the cracker’s demise
again began to swirl in recent days, culminating on Tuesday, when
Mike Graney, executive director of the West Virginia Development
Office, reportedly told lawmakers that Braskem had indicated it
would not build the plant. He told state lawmakers on the Joint
Committee on Natural Gas Development that Braskem is “quietly
marketing the property and that the property is for sale,” said
Delegate John Kelly, co-chair of the committee.
“It’s a big deal…that’s something
we’ve been pretty hopeful for for development for sometime,” Kelly,
who represents Wood County where the property is located, told
NGI on Wednesday. “But it’s been dragging on and on, and there
hasn’t been a lot of activity. There’s been some rumors and denial
of rumors as to whether it was going to proceed or not. But there
really hasn’t been much activity on it.
“At least if they’re not going”
to build it, “they’re trying to market it to other folks who would
have a similar interest in it,” he added.
A state Commerce Department
spokesman referred questions to Allentown, PA-based McGowan
Corporate Real Estate Advisors. Braskem said it would have no
further comment at this time.
TopLine Analytics’ Tom Gellrich,
founder of the Philadelphia-based consultancy that is focused on
downstream development, said Braskem’s parent company Odebrecht SA
has faced trouble that likely impacted the West Virginia project.
Gellrich said many in the petrochemical industry thought Braskem
would be sold, but when a deal fell through, the cracker’s prospects
dimmed.
Plans for the facility were
complicated further when conglomerate Odebrecht was embroiled in a
corruption probe involving Brazilian oil giant Petroleo Brasileiro
SA, aka Petrobras. Odebrecht agreed with U.S. authorities in 2016 to
pay billions in international fines for its role in a bribery
scandal involving politicians and other officials to secure
contracts with Petrobras.
LyondellBasell confirmed in June
that talks with Odebrecht to buy Braskem had ended, stating that
only after “careful consideration” did management decide “not to
pursue the transaction.” Odebrecht, Braskem’s controlling
shareholder, had been counting partly on a sale of the company to
resolve debt issues created by the corruption charges. It filed for
bankruptcy protection last month.
“Now the question becomes how
does Odebrecht and its various subsidiaries come up with the money
to pay these fines?” Gellrich told NGI. “They have no
options” even in bankruptcy. “So, what’s going to happen with
Braskem? This is very interesting. And Braskem is getting rid of
some of its assets, and I suppose they will sell their rights to the
land they were going to build the cracker on.”
Gellrich, who once worked as a
petrochemical executive for ExxonMobil Corp. and Total SA, which
over a decade ago spun-off global chemical company Arkema, said
Braskem could still be sold. He said the company is more attractive
than some of Odebrecht’s other holdings because of its international
profile.
In the meantime, there’s still
likely to be interest in the West Virginia site from other chemical
manufacturers. For decades, the Braskem-owned property in
Washington, WV, near Parkersburg has been home to chemical plants
once operated by GE Plastics and Borg Warner Chemicals. Most
recently, Saudi Basic Industries Corp., aka SABIC, had operations
there.
“The property is probably one of
the best shovel-ready sites that we have anywhere along the Ohio
River,” Kelly said of a corridor pocked with brownfield sites that
is being marketed for energy development. The site has highway
access, barge loading facilities, rail infrastructure and can easily
tap the electric grid.
“I think it’s a marketable site,
and if Braskem doesn’t do something there, I think somebody else is
going to do something there,” Kelly said. “And from what I
understand, there might be some interest in the property already.”
While PTT Global Chemical pcl (PTTGC)
and Royal Dutch Shell plc are further along with their Appalachian
ethane cracker projects, and as polyethylene and other petrochemical
exports are poised to boom with a buildout on the Gulf Coast,
Gellrich said it might not appear that there’s room for another
plant in the Northeast. But he noted that the basin has advantages
that could still be attractive to a buyer.
Low-cost feedstock, shipping
advantages, cheap energy prices and geographical benefits are all
things that have attracted Shell and PTTGC to the region, Gellrich
said. Shell is
currently building a multi-billion dollar ethane cracker in
western Pennsylvania. Meanwhile, PTTGC is
thought to be close to a positive final investment decision for
a large cracker in southeast Ohio as it continues to make progress
on a site there.
“Shell and PTTGC, and potentially
others at the Braskem site, are in an interesting position,”
Gellrich said. “They can sell to the local market.” Shell has said
that although the bulk of refining capacity is on the Gulf Coast,
70% of the nation’s polyethylene consumers are within 700 miles of
the Mid-Ohio Valley, a region that includes parts of Ohio,
Pennsylvania and West Virginia.
Business manager Nathan Lord of
Shale Crescent USA, which was formed three years ago to better
market the region for energy development, said Appalachia can
support up to four more crackers in addition to Shell’s facility,
“as far as the supply of ethane is concerned.” He was referring to a
study commissioned by Pennsylvania that showed the region is
ripe for petrochemical development.
Smaller-scale ethane crackers
that also have
been proposed for Appalachia have been on the backburner for
years, failing to gain any traction since they were announced. Even
still, Lord told NGI that the larger Braskem site could
ultimately attract a buyer.
“Does that mean it’s going to
happen? Certainly not,” he said, “but when you look at the economics
and the opportunities, it makes sense to build future crackers
here.”
Sep 9, 2021
Brazil's Braskem to consider Thailand JV with
SCG Chemicals
Brazilian petrochemichals company Braskem SA on Thursday said it has signed an
agreement with SCG Chemicals to consider a joint venture to invest in a
bioethanol dehydration plant in Thailand.
The venture would produce bioethene and polyethylene
in a plant in Map Ta Phut, Rayong, Braskem said in a securities filing. The
project is alligned to the company's goal to reach carbon neutrality by 2050, it
added.