PRESIDENT Online 2022/08/09
6万社の下請けが不要になる…「おもちゃのように車を作る」というテスラ方式はトヨタ方式を超えられるのか
自動車のものづくりを根底から変える「ギガプレス」
電気自動車大手テスラの製造方式は、トヨタなど既存の自動車メーカーとはまったく異なる。経営コンサルタントの竹内一正さんは「テスラは『ギガプレス』と呼ばれる大型の鋳造機を使って車のボディを溶接なしで作っている。こうした常識破りを繰り返すことで、テスラは爆発的な成長を続けている」という――。
「おもちゃの車を作るように、フルサイズの車を作る」
自動車は約3万点に上る部品の集合体だ。トヨタなどの自動車メーカーは、膨大な数の部品をすり合わせ技術で統合し、快適な乗り心地と信頼性を実現してきた。ところが、イーロン・マスクはこの部品の集合体であるクルマを、「文字通りおもちゃの車を作るのと同じように、フルサイズの車を作ろうとしている」と語っている。
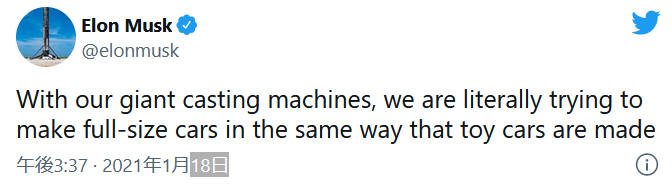
テスラのSUV「モデルY」のリア部のアンダーボディは、アルミ合金の一体鋳造で作り出している。モデル3の車体下部はフロント、バッテリーパック、リアの3つで構成されていて、リア部のアンダーボディは後輪のサスペンションなどを構成する部分になる。
モデル3のアンダーボディの一体鋳造を可能にしたのは全長20メートル、総重量400トン強の巨大な鋳造機「ギガプレス」だ。イタリアのIDRA社が製造したギガプレスは、高温で溶融したアルミ合金を金型に流し込んで型締力6000トンで成型する。
ギガプレス登場以前のモデルYのリア部のアンダーボディは、70回におよぶプレス加工、押出成形、鋳造を必要としていたが、それをギガプレスは約100秒で一気に作ってしまう。ギガプレスを使うことで、「製造スペースを30%削減し、約1000台あったロボットから300台を削減できた」とイーロンは胸を張った。
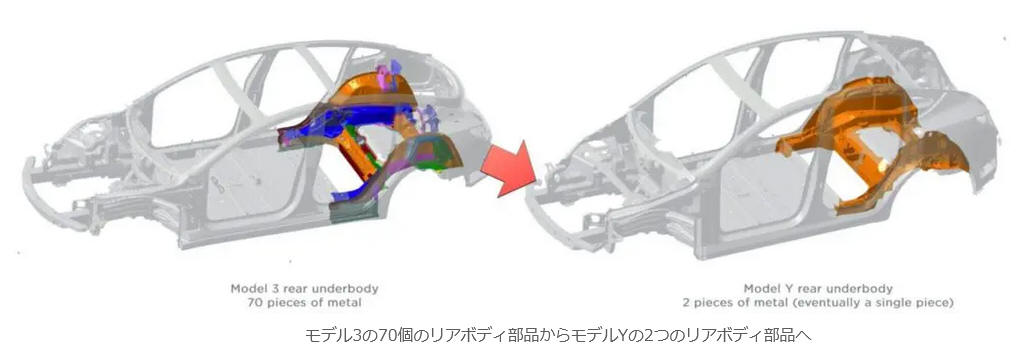
https://lowcarb.style/2021/12/05/tesla-megacast-2/
すでにテスラはモデルYのリア部だけでなくフロント部のアンダーボディもギガプレスで一体鋳造して作り出しており、製造コストは40%削減が可能となった。
まさに、おもちゃの車を作るように、フルサイズの車を作りつつある。これは自動車のものづくりを根底から変える可能性がある。
約6万社の下請け企業を抱えるトヨタには導入できない
日本の経済を支えるトヨタはクルマの約3万点の部品を、約6万社の下請け企業から調達している。だが、生産方法が変わったからといって、トヨタが彼らの仕事を簡単に切るわけにはいかない。
つまり、もしもトヨタがギガプレスを導入したら、長年にわたり関連パーツを納入していた数々の下請け企業が経営危機に直面するだけでなく、トヨタが支えてきた日本の自動車の産業構造そのものを揺るがしてしまう危険性さえある。
数々の困難を乗り越えて完成したギガプレス
テスラSUVの「モデルY」のベース車両である「モデル3」のリア部は、約100個の部品を溶接や接合で複雑に組み上げていたが、イーロンはそれが気に入らなかった。「もっとシンプルにならないか」。そこで、1つの作業で作り上げるギガプレスの構想が浮かんだのだった。
さっそくイーロンたちは大手の鋳造機メーカー6社を選び出し、アンダーボディの一体鋳造のアイデアを持ち込んで、可能性を打診した。ところが、6社中5社から即座に「無理だ」と回答された。
イタリアのIDRA社だけがかろうじて前向きな姿勢を示してくれた。それでも「たぶん」という程度の頼りない返事でしかなかったが、失敗を恐れないイーロンにとってそれは「できる」と同じだった。
しかし、アンダーボディの一体鋳造は簡単にはいかなかった。
例えば、アルミ合金が冷める段階で熱変形が起こり、設計寸法どおりにできなかった。製造条件をいろいろ振ってはトライアル・アンド・エラーを繰り返していった。言ってみればそれはモデルY側の設計領域で譲れる部分と、ギガプレス側の鋳造工程でチャレンジする部分の交差点を見つけ出す作業だった。
さらに、従来のリア部アンダーボディをそのままの形状でアルミ合金の鋳造品に置き換えただけでは、車両が衝突した時の衝撃強度が十分ではない。そこで、テスラは「変形制御ゾーン」と呼ぶ、一体鋳造部が段階的に衝撃を吸収していく独自設計を生み出した。これについては、「一体型エネルギー吸収鋳物
'Integrated Energy Absorbing
Castings' 」という名称でテスラは特許を出願していた。
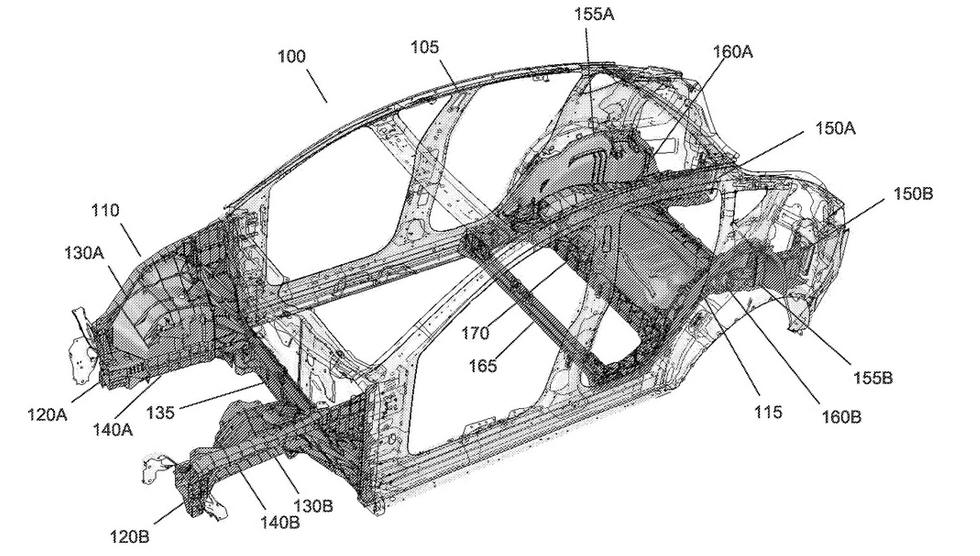
結局、テスラがIDRA社と協力してギガプレスの実用化を進めてものにするまでには、1年以上の時間を費やした。
現在テスラは新型車「サイバートラック」にもギガプレスを使う考えで、それは型締力が9000トンとさらに強力な鋳造機が必要となる。
そのほかのEVメーカーもテスラ方式に舵を切っている
「ギガプレス」はテスラの専売特許ではない。
2030年までにすべての新車をEVにすると宣言したスウェーデンのボルボ社も、テスラと同様にギガプレスによる一体鋳造方式を採用する計画だ。次世代EVのために数年間で約1300億円を投じるボルボのトルスランダ工場にはギガプレスが導入され、次世代EVプラットフォームの製造に活用される。
さらに、中国の自動車メーカーでもギガプレスへの動きを見せている。
2014年に創業したNIO(上海蔚来汽車)だ。NIOは新興EVメーカーだが、自動運転開発にも力を入れていてシリコンバレーに開発センターを有し、先進運転支援システム「NIOパイロット」を搭載した車種も現在市販している。
そのNIOが型締力1万2000トンの超大型鋳造マシンを使ってEVの製造を行うようだ。テスラがモデルYで使っているギガプレスの型締力が6000トンだったのに対し、NIOが計画している超大型鋳造マシンは2倍の型締力になる。詳細はまだ判明していないが、ギガプレスが世界の自動車メーカーの生産方式の主流となるのか、注目が集まっている。
修理費用が従来よりも大幅に高くなるデメリットも
ギガプレスは自動車メーカーのものづくりを変えるのか? テスラファンやEV推進派はギガプレスを高く評価している。
一方で、ギガプレス懐疑派も多い。たとえば衝突事故になった時、アンダーボディのアルミ製鋳造品をすべて交換する必要があり、修理費用は従来より大幅に高くつく。損傷具合によっては廃車となる恐れも高い。それに対し、従来の鋼材と溶接の組み合わせなら、部分的な修理ができるので、修理費用は総じて安くなる。
では、その事態を自動車保険でカバーしてはどうか? 可能だろうが、クルマの保険代が値上がりするのではないか。
ここで少し立ち止まって考えてみよう。
新しいことを始めると、常にネガティブな意見は出てくるものだ。新しいことは100点満点ではない。起こりうる問題を事前にある程度想定しても、やってみなければわからないことのほうが多い。
すると、会議に次ぐ会議となる。泥をかぶりたくない上司や、責任を取りたくない経営陣の下では、リスクを嫌う圧力がのしかかり、議論は結局振り出しに戻って、従来の方法の維持に落ち着く。
こうして日本は失われた30年を過ごしてきたのではないか。
テスラ方式とトヨタ方式のどちらが生き残るか
イーロン・マスクの経営姿勢は、一言でいえば、「リスクを積極的に取る」。その結果、新たなことに挑んでは、スピードの速さと、スケールの大きさを実現してきた。
テスラのEV出荷台数は08年ではたった100台程度だったが、13年後の2021年には約100万台で1万倍の成長を遂げた。2013年の世界のリチウムイオン電池の総生産量を超える能力を持つギガファクトリーを2014年にネバダ州で着工すると、2019年にはギガ上海、次いでギガベルリン、ギガテキサスと巨大工場を瞬く間に展開していった。
だが、その間には、ロードスターもモデルSもモデル3も立ち上げで混乱し、経営危機にも瀕した。テスラ自慢の自動運転オートパイロットは交通事故問題で米当局から調査のメスも入っている。
だが、トラブル続きであってもイーロンの事業スピードはますます高速化し、だからこそ、ネガティブな反応はイーロン・マスクが進む先でいつも付いて回っていた。
思い起こせば2008年テスラがロードスターを出した時、汎用のリチウム電池を数千個も搭載したEVという設計思想そのものに悲観論が相次いだ。当時の自動車メーカーは専用の大きなバッテリーを開発していたからだ。なにより、バッテリーセルを数千個も使う構造だと、もし1つのセルで品質問題が起きればバッテリー全部がダメになってしまうと多くの業界関係者、専門家が危惧していた。
それでも、テスラは独自設計でその不安を払拭した。気づけば、どの自動車メーカーのEVもリチウム電池を大量に搭載するテスラ方式に追従していた。
イーロン・マスクが進める巨大な一体鋳造機ギガプレスが、クルマ作りの本流となるかどうかは現時点ではまだわからない。「おもちゃの車を作るように、フルサイズの車を作る」と大風呂敷を広げたイーロンの本当の正念場はこれからだ。だが、もしイーロンの狙い通りになった時、6万社の下請けを抱えるトヨタはどう出るのか。今後に目が離せない。